Hydroforming Services
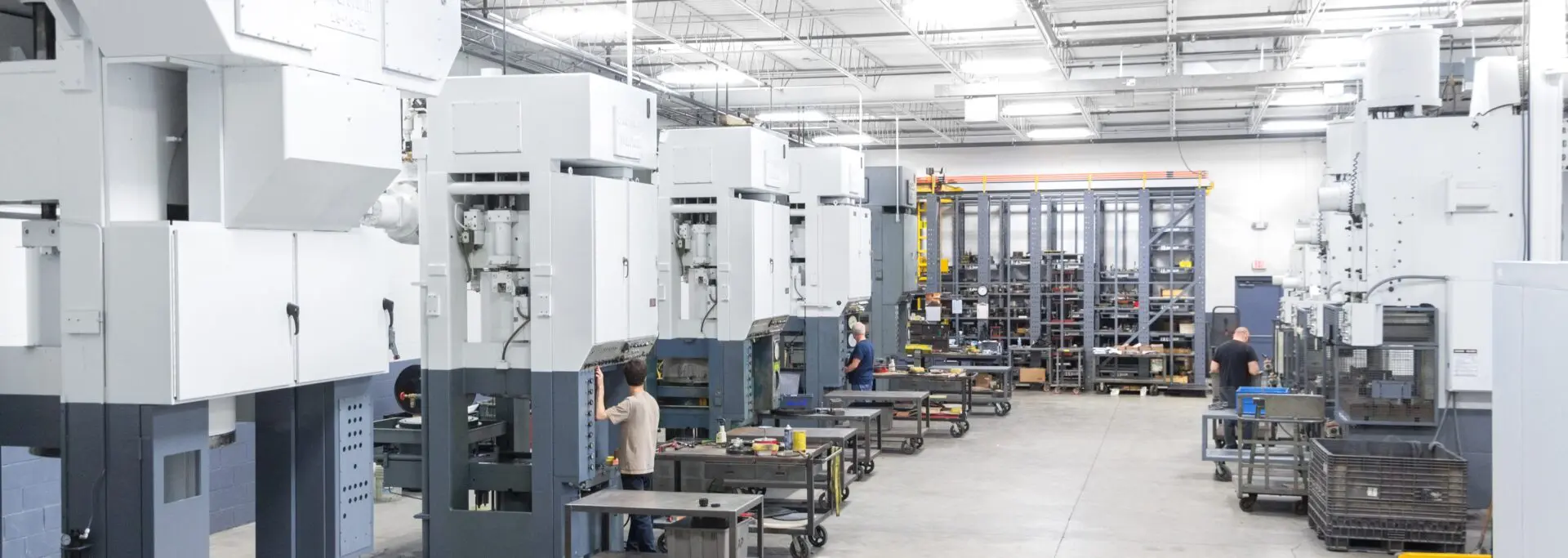
What is Hydroforming?*
Hydroforming is used specifically for cost-sensitive short to medium volume metal forming applications. Hydroform presses use simple, inexpensive tooling and accurately controlled hydraulics allowing for a total cost advantage over conventional press equipment. In fact savings can be realized in prototype design and production, numbers of operation, depth of draw, draws of irregular configuration, exotic metals , material costs, annealing, metal thin out, tolerance, accuracy, finishing costs and others.
Controlled pressure fluid forming offers the most effective deep drawing technique available today. Unlike hydraulic and mechanical presses, fluid forming does not require costly matched die sets, nor is a moving blankholder and ring necessary. The dimension and shape of the draw are limited only by the volumetric capacity of the forming chamber.
Download more information on Hydroform press principals and forming cycles
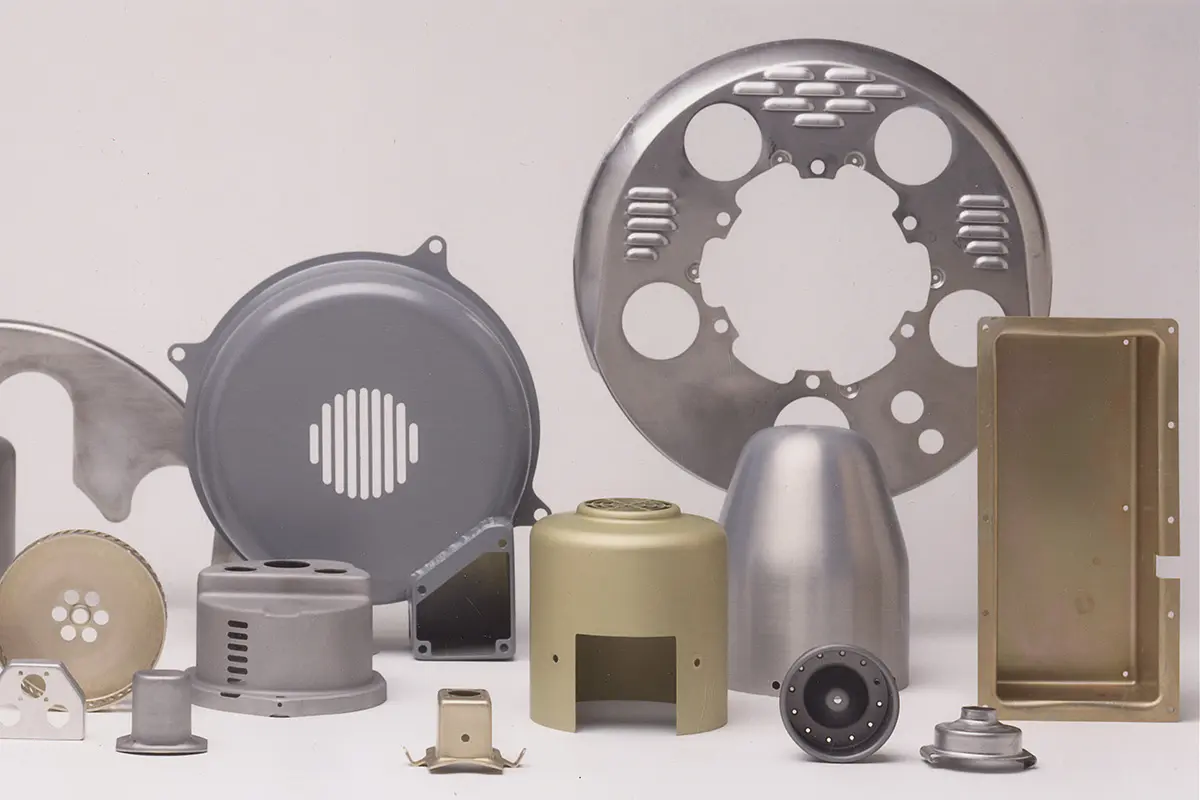
Advantages of Hydroforming
The advantages of the hydroforming process include low tooling and part development costs, reduced set-up times and finishing costs. Traditional deep-draw tooling is manufactured to process a specific material thickness, while hydroform tooling can accommodate multiple material thicknesses without alternation. Material types and thicknesses can often be changed utilizing the same tooling.
The Economics of Hydroforming
Hydroforming substantially reduces production and operating costs. “Savings up to 30% on material costs, 75% on finishing costs and 90% on tooling costs are not uncommon. Additionally most shapes can be manufactured in one operation.
Tooling, Materials, Quality & Costs Savings
- Simplified tooling, only a male punch and blankholder are required. This reduces engineering and manufacturing. (No die maker’s fit necessary). Moreover, punch materials are relatively inexpensive – mild steel, inexpensive tool steel and cast punches of iron, brass, plastic, steel or aluminum can be used.
- Complete tool changes can be made in a matter of minutes. Tools are quickly mounted and self-centering and -aligning. And tool installation is quick and simple. (Quick change diaphragms – single piece diaphragm cartridge and punch)
- Flexible female die minimizes or eliminates “shock Lines” or “draw marks” reducing finishing costs.
- Controlled blankholding permits savings in blank size and uniform thin-out permits as much as 25% reduction in stock gage requirements offering better material utilization
- Continuously controlled forming pressure minimizes thin-out, permitting a higher percentage of reduction and so few operations are required
- Parts retain higher mechanical and physical properties because material is uniformly worked during the draw which offers improved part quality
Versatility
Hydroforming allows for the manufacture of “a wide range of complicated parts that would be impractical and” even “impossible to produce by other methods.
(Adaptability to) Single action presses using conventional tooling increases options for drawing, compacting, embossing, coining, flattening and similar applications.
* Content on this page was curated from the Verson Hydroform Presses brochure, Bulletin No. HP-82, 1981